These are things that I deal with during virtually every project now, but I wish I saw some of this advice in my early research.
Existence of interfacing
The fact that interfacing exists and is so common-place in so many patterns really threw me for a loop when I first got started! I don’t know where I thought the structure in things like blouse cuffs came from, but I also never took apart my garments to look, so who can blame me ;)
It was frustrating, because in addition to making sure I had enough fabric, thread, and other notions for sewing a garment, I also had to make sure I had enough interfacing and the right type of interfacing for a project.
AND on top of everything, I started sewing when COVID was starting to spread globally. During this time, a lot of people were using interfacing as a filter layer in facemasks, leading to shortages and exorbitant prices for interfacing that I could find in small increments on places like Etsy.
Availability is no longer a challenge (fortunately), and I’ve gotten a chance to try different types of interfacing, which I think was a net positive in helping me learn more about the resources at my disposal and how they affect a garment’s overall look.
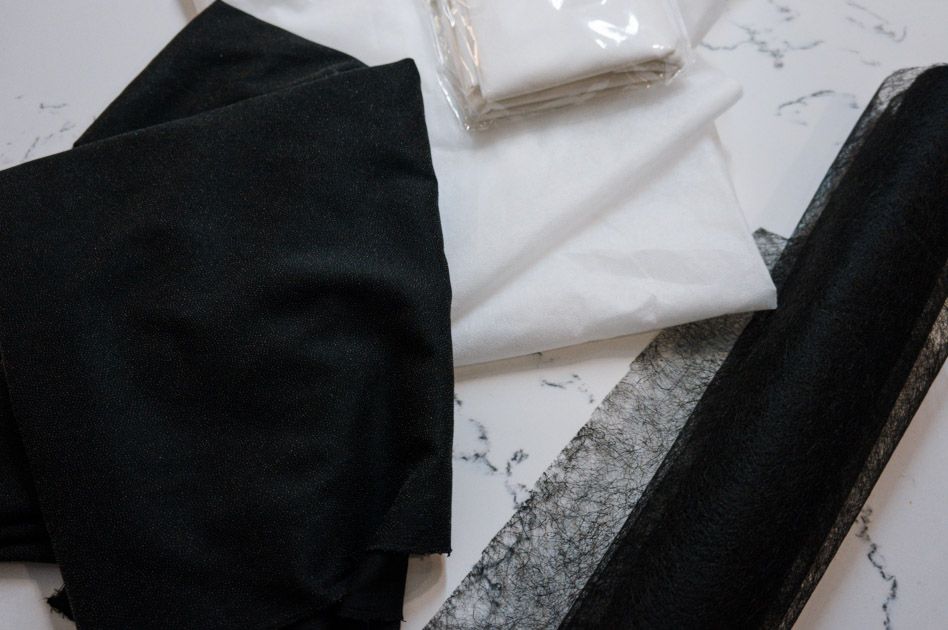
A needle has a short lifespan
I have a set of sewing needles that I bought more than a decade ago that I kept around for small fixes and mending before I started learning to sew. I never even thought of changing them out, or that they would get dull (or that the dullness would somehow affect performance!)
To be honest, I still am not sure if it makes a difference for hand sewing, but it sure makes a HUGE difference for machine sewing!
I’ve seen tips to dispose of a needle after every project, and I now have a collection of machine needles for different fabric types and of different widths. I don’t necessarily follow the change-needle-after-every-project advice, but it’s a really good troubleshooting step to try if I start having issues like the machine eating my fabric, or if a needle breaks.
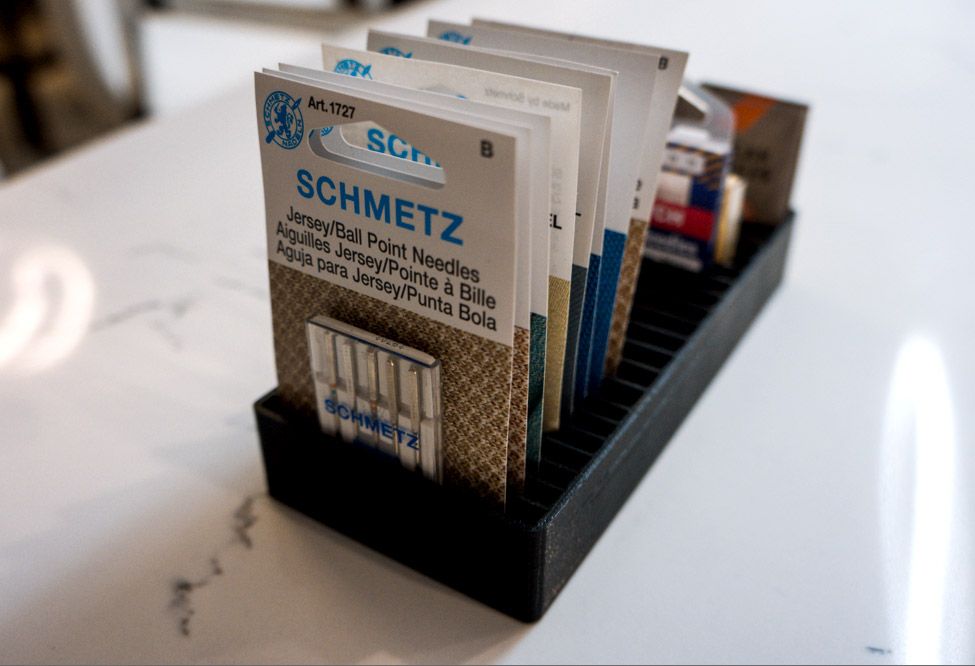
Not all thread is created equal
If someone had told me a year ago that I would have strong opinions about thread brands, I’d look at them like they were crazy.
I have these strong opinions because I had a very painful (metaphorically) first experience of using low-quality thread that I bought purely because it came in a large volume of many colors. I proceeded to sew a horribly frustrating first project that was chock full of the fabric getting stuck in the machine and many broken needles. As soon as I changed the thread to a higher quality, the issues miraculously resolved themselves!
Since then, I stick to only German-made thread. With all the things that could potentially go wrong, it’s not something I want to spend my energy being frustrated on!
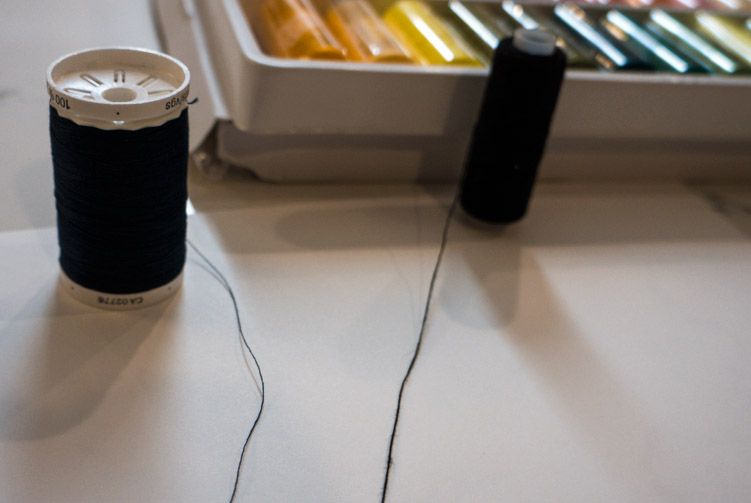
A yard of fabric is not created equal
My mom is a gifted seamstress, and I would often go with her to the fabric store when I was younger and watch the fabric getting cut on the cutting table in yard increments. When I started sewing, myself, I thought “aha! A yard, that’s easy and consistent!” but alas, even though a yard is the standard measure of fabric, the width of the fabric can fluctuate wildly. My stash has fabric pieces that are 44” wide, and some that get up to 70” wide. When you’re trying to estimate the fabric you need for a project, you can cut out way more pieces from a yard of fabric that’s 70” wide, than a yard that’s almost half that width!
Although many pattern makers are considerate of that and include some common fabric widths in their required yardage estimates, there’s some amount of guesswork I end up doing when planning a project and my fabric doesn’t match up with the standard widths.
The fun continues when I peruse patterns that provide metric measurements (meters and centimeters), where I not only need to convert meters to yards (OK, I know they’re super close and I shouldn’t complain), but also convert the centimeter fabric width to inches.
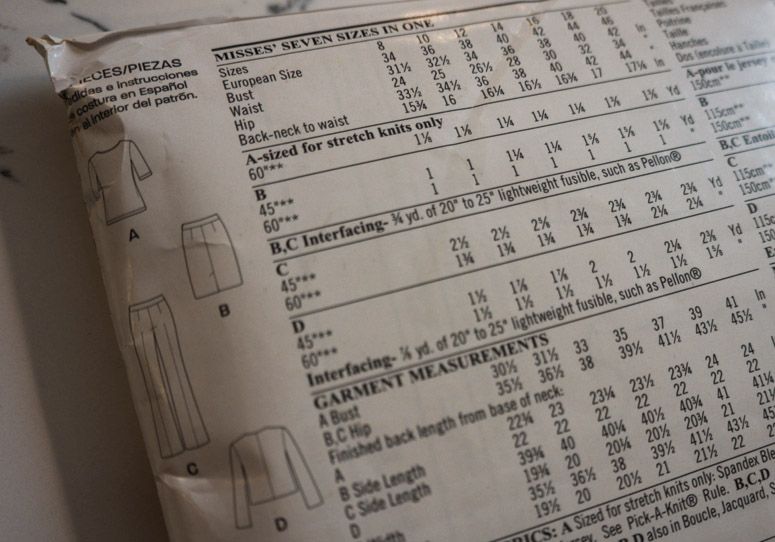
Importance of thread management
I’m not talking about holding the threads when you first start a machine stitch, or following good threading practices on your machine. I’m talking about the thread trimming that you cut off that multiply in volume at a rate that surpasses that of tribbles, rabbits, and mice.
At first I’d just keep a little pile of trash threads and other cloth trimmings near my machine, but after my garment accidentally getting into that pile and knocking it on the floor, I learned my lesson. I now put my sewing trash into a little cloth bowl that a friend kindly made for me, which really cuts down on the random threads making their way around the house (although I am by no means free of that ;)).
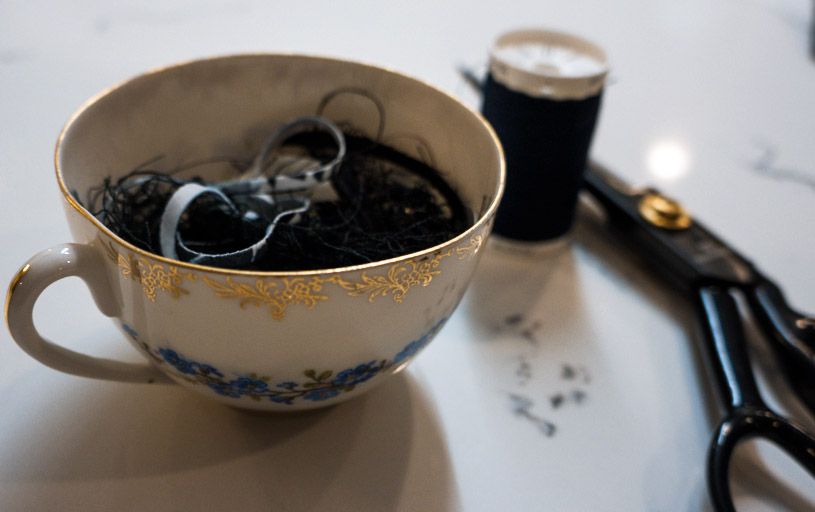
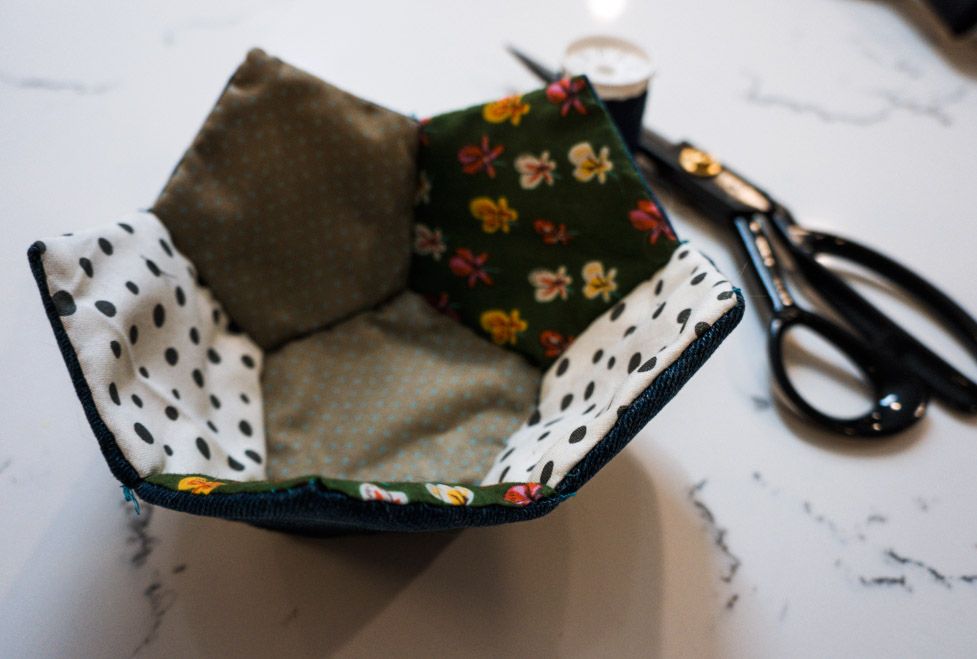
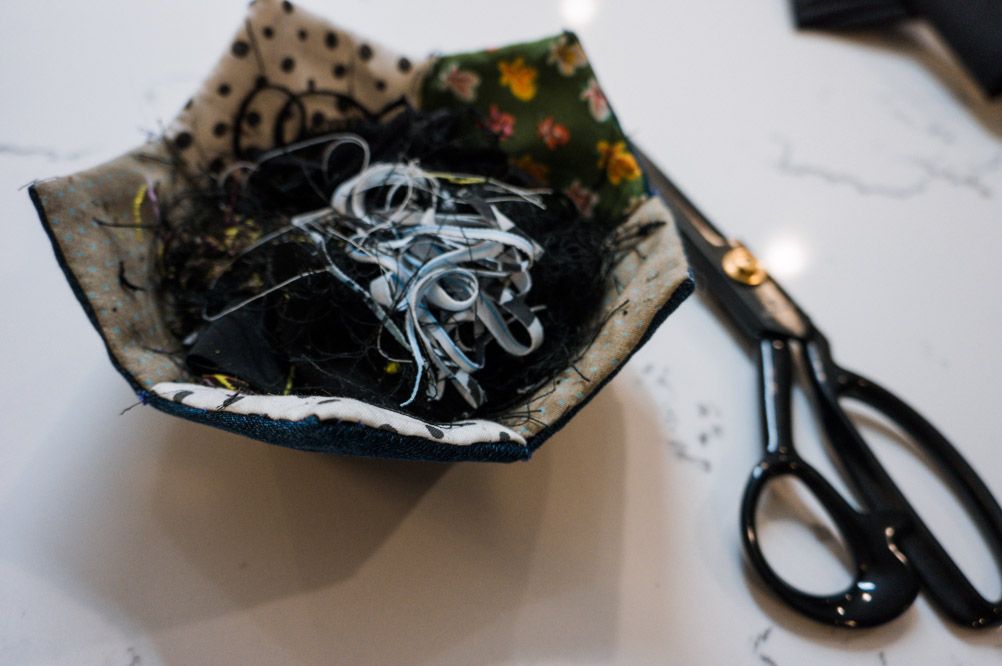
I hope that these tips help save some frustration in your sewing journey!

Comments powered by Talkyard.